With the steering column extended whilst I collected
the parts from Dax, I was able to get this installed. One slight
spanner in the works was that I had not been supplied with the lower
column bracket for use with a V8, however one arrived next day in the
post. Everything seemed to fit as required, however I found that I
didn't need to grind anything off the engine mount as there was about
10mm clearance, despite other build diaries reporting that grinding to
the mount was necessary to allow clearance. Although it seems trivial it
was quite an achievement to turn the steering wheel and see the steering
rack move.
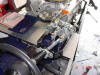
Although the front axle shouldn't really be fitted
until the side panels are in place (which can't be fitted yet as I need
the exhaust first), I thought it best to be able to get the wheels on
and be able to move the car out of the garage if needed. After the
performance with fitting the bushes into the A frame, the heavy duty
vice was used again to push the ball joints into the lower wishbone.
These were fitted with little effort once I'd managed to get everything
lined up in the vice, using sockets as spacers. The hardest part of
assembly was fitting the front mudguard brackets intro the hub carriers.
After trying a rubber mallet to knock the bracket into the opening,
resorted to a lump hammer and plenty of cardboard to protect the chrome
plating. After following the Dax manual for the first side, I found it
easier on the other side to attach the upper ball joint to the hub
carrier first before attaching it to the upper wishbone. After all
the effort on the front end, I thought I'd have a go at attaching the
dashboard. This will need trimming slightly around the steering column
surround, although decided to leave that for another day and put the
dashboard in the loft.

Whilst waiting for the wheels to arrive, which were
due anytime now, a pedal box cover was fabricated. I had bought a piece
of aluminium from B&Q previously which although expensive (about £7 for
a 500x500 piece) seemed ideal for making up the cover. Although only
thin It could be cut with a stanley knife and was rigid enough when
folded into a box. Holes were cut for the pedals and it was pop riveted
into place before bolting the pedal box into position.
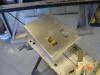
The wheels arrived the next day, although this
brought about the dilemma of whether the sierra studs were long enough.
Having tried the wheels for size, it was obvious that although the
original studs allowed the nut to be attached, it would be better to
have them 5 to10mm longer. Larkspeed in Leeds had extended studs in
stock and at £1 each incl VAT seemed quite reasonable. These were cut
down to 52 mm long. (the photo below shows from left to right original
sierra 42mm stud, extended stud cut down to 52mm, 62mm extended stud). I
was pleased to find that the Dax price for the Image wheels had included
chrome wheel nuts and a jar of resin wheel protector.
Next task was to fit the rear wiring loom so that the
rear tub could be fitted. The rear wiring loom didn't seem long enough
to route around the rear chassis and in the end was routed over the
petrol tank which although it won't be seen wasn't as neat as I would
have liked. The wires to the petrol gauge sender and pump were split
from the loom to aid routing of the cables. The loom was taking along
the top chassis rail of the transmission tunnel and up through an
aluminium bracket (borrowed from an idea from Chris Bell's web site).
Whilst the centre cover was removed, I took the opportunity to bolt the
propshaft to the gearbox. I had ordered the correct bolts from Rimmer
Bros. The holes within the propshaft needed enlarging slightly (by about
1mm) to allow the bolts to be fitted, which wasn't the easiest of things
to do with the propshaft in place. It seemed another achievement had
been reached being able to roll the car outside and work on it in the
sun. This seemed to attract a few comments from passers by, which
started me thinking about insurance, given the amount of money that has
gone into the car so far. A quick phone call to Adrian Flux and £150
later and the car was insured.
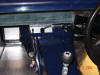
The rear tub could now be fitted. Aided with a number
of clamps and use of the jack and piece of timber to support the
underside, the tub was positioned. The chassis rails around the fuel
tank were marked on the inside face of the GRP with a permanent marker.
The tub was then removed and ideal position of fixings marked on the
inside. A 2mm drill bit was used to drill pilot holes through from
the inside and these were then enlarged, drilling from the outside face,
to suit the hex head self tappers being used for fixing. The tub was
then offered up again for marking of the holes on the chassis and
removed for drilling. Finally, after applying plenty of Sikaflex, the
tub could be fixed into position.
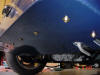
With the rear tub fixed, the filler cap and hoses
could be fitted. The top of the filler cap was fitted 60mm down from the
top of the tub to allow clearance should a cover / softtop be fitted
later. A core cutter was used to cut the main hose and a dremel with
sanding attachment used to notch out for the vent pipe. The main problem
with fitting the hoses was with fitting the smaller vent pipe as the
pipe was not flexible enough to fit without kinking and distorting. This
was resolved by shortening the solid stub connection from the tank,
which was cut using a hacksaw. A piece of kitchen paper was inserted
into the pipe first to stop any debris getting into the tank. Whilst
working on the rear end of the car, the lights were fitted. The circular
fog and reversing lights supplied now by Dax were reasonably
straightforward to fit. A 56mm core cutter was used to drill the holes
first, and the lights stuck into position using Sikaflex, remembering
that the lenses need to installed at 90 degrees to the ground.
The Dax build manual states that fitting of the
windscreen wipers is straightforward, however I was struggling. I
couldn't seem to get the wiper boxes to fit, until after a phone call to
Dax, it was apparent that the spacer tubes for fixing the wheel boxes in
place were from a Tojiero. With the correct spacers, the wiper system
was installed and the position for the aluminium bracket marked and
stuck into place. With the wiper motor fitted, there was nothing else I
could do with the scuttle until the heater arrives, so turned my
attention to the battery shelf. The expansion tank and battery tray were
fixed to the shelf using rivnuts. The components fixed to the bulkhead
were only trial fitted as they will have to be removed to fit the
aluminium panel.

For the aluminium panel for the bulkhead, I ended up
buying more aluminium from B&Q - maybe expensive at £15 for a 500x1000
sheet, but at least convenient. At 0.5mm it wasn't particularly thick
put would be adequate when attached to the GRP. For the first attempt at
cutting out the panel I used a jigsaw with fine cutting blade which gave
the right shape but buckled the panel slightly. As there was enough
material for two, I used the first one for a template to cut the second
this time scoring the surface several times with a stanley knife which
produced the desired effect. Whilst at it, decided to fabricate a panel
for the indent behind the master cylinders. To tidy up the front edge of
the battery shelf and top edge of the footwell closure panels a 10x10
aluminium angle was stuck into place.
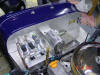
Having bought a Mocal remote oil filter kit, I had
ended up with a set of hoses with 90 degree fittings which didn't seem
long enough and restricted where the filter could be fixed because the
fittings always ended up pointing in the wrong direction. Whilst reading
the Think Automotive catalogue to order some new pipes and fittings, I
noticed a section on how to alter the angle of the connections on the
ready made sections of pipe. By holding the end of the pipe in a vice it
was possible to turn the fitting to point in the desired direction.
Having done this, a bracket was fabricated out of 3mm aluminium plate
and pop riveted into position.
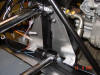
A 9.5mm rubber fuel hoses was used to connect from
the fuel tank connection to the pump. Although a bit tight, the fuel
hose did eventually go onto the fuel tank connection with the help of a
squirt of WD40. Quite a bit of thought went into the routing of the fuel
pipe along the transmission tunnel. It would have been easy to mount the
pipe to the underside of the chassis but I wanted to protect everything
where possible in the event of grounding. The pipe was clipped at close
centres around the gearbox mount and the handbrake cable to prevent
rubbing. Whilst the tunnel cover was removed, I core cut a hole for
gaining access to the gearbox oil filler point. The hole was filled with
a 50mm rubber blanking plug that had bought from a trade stand at the
Newark show.
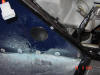
I started off wiring the column switches with the
intention of converting the loom to use the newer Sierra mark 2
switches, given that I had been collecting a selection of them at
various shows over the past 6 month and had chosen 2 suitable for use.
However having looked into the method of converting the dax loom on the
Rushowners archives the problem seemed to be changing the headlamp
switching from negative to positive switching or vice versa, which also
meant altering and adding relays. As a last chance solution before
attacking the loom I went to Malley's Ford Spares in Leeds who had a box
full of both switches. I even managed to find a wiper switch without the
intermittent wipe function, and an indicator switch without the horn
button for £5. Both fitted and worked without any problem, although the
wiring was altered slightly to incorporate the steering wheel horn push,
following the notes in the build manual. I managed to salvage the
ignition wiring connector and horn wiring connector from the
original Sierra wiring loom. Whilst at it, the horns were fitted,
just in front of the oil filter. What an achievement that night,
switches and horns working - not sure the neighbours were too pleased to
hear I had got the horn working at midnight !
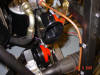
|